Advanced Metal Stamping Techniques for Precision Manufacturing
Advanced Metal Stamping Techniques for Precision Manufacturing
Blog Article
Unlocking the Power of Steel Stamping: Methods for Improved Item Advancement
In the realm of manufacturing, the application of metal stamping holds a significant location as a result of its adaptability and efficiency in generating intricate components and elements. However, the real potential of steel marking stays untapped by many companies seeking to boost their product growth procedures. By checking out advanced methods and methods tailored to maximize layout, product option, production performance, and high quality control, companies can unlock a wide range of possibilities to raise their items to new elevations of development and efficiency.
Advantages of Steel Stamping
Steel marking deals a economical and efficient technique for generating premium steel elements. This manufacturing process includes shaping, reducing, or developing steel sheets utilizing a marking press (Metal Stamping). One of the vital advantages of metal marking is its capability to produce complex geometries with high precision and consistency. This is specifically advantageous for sectors such as auto, aerospace, and electronics, where detailed steel components are frequently called for.
Additionally, metal marking permits for high-volume manufacturing, making it perfect for projects that call for big quantities of metal parts. The rate and repeatability of the stamping process not only ensure price financial savings however also contribute to faster turnaround times for manufacturing orders. Additionally, the use of automatic equipment in metal marking helps reduce the threat of human mistake, causing boosted general product top quality.
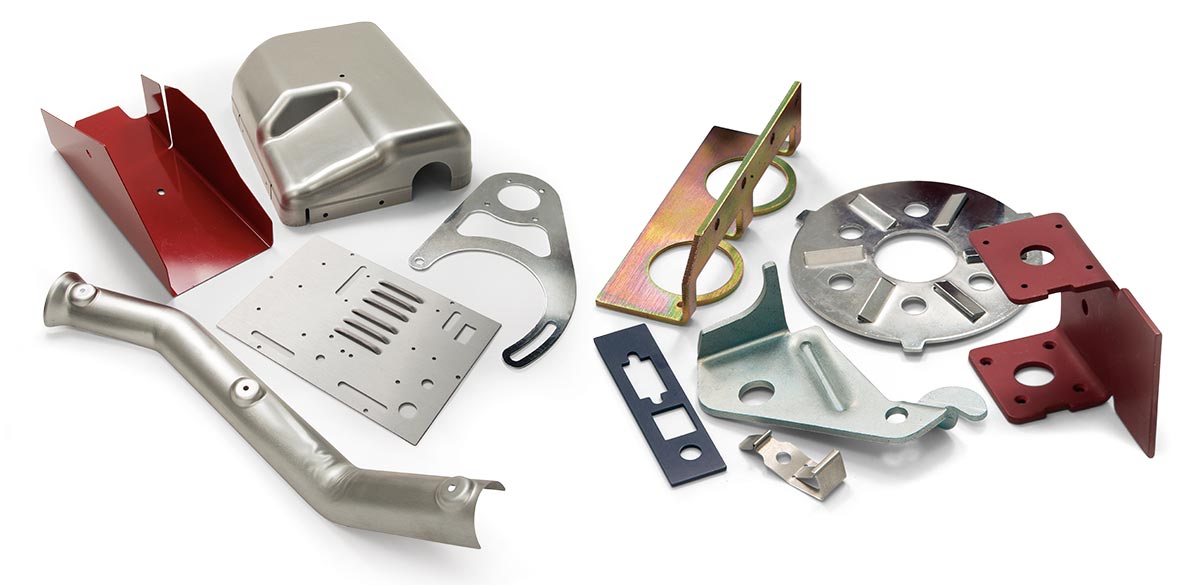
Style Optimization Methods
With cautious consideration of material properties and geometric configurations, style optimization methods play an essential function in enhancing the performance and functionality of metal stamping processes. By purposefully evaluating variables such as product thickness, type, and stamina, makers can customize the style to make the most of the performance of the stamping operation. Utilizing simulation software application, engineers can forecast exactly how various layout variations will behave under different stamping conditions, enabling the recognition of potential problems before manufacturing begins.
Furthermore, integrating functions like fillets, chamfers, and embosses right into the design can improve the general top quality of the stamped component while reducing the risk of issues such as splitting or contorting. Furthermore, maximizing the format of attributes on the part can improve the material circulation during marking, causing more regular and specific outcomes.
In essence, design optimization methods allow suppliers to adjust their metal marking procedures, bring about enhanced item high quality, raised manufacturing performance, and eventually, a much more competitive position on the market.
Product Choice Methods
Style optimization strategies in metal marking procedures heavily depend on calculated material selection approaches to ensure the preferred efficiency and efficiency of the manufactured components. The choice of product in metal stamping is vital as it directly affects the quality, sturdiness, and general performance of the end product. When choosing the ideal product for a details project, elements such as mechanical properties, rust, cost-effectiveness, and formability resistance must be thought about.
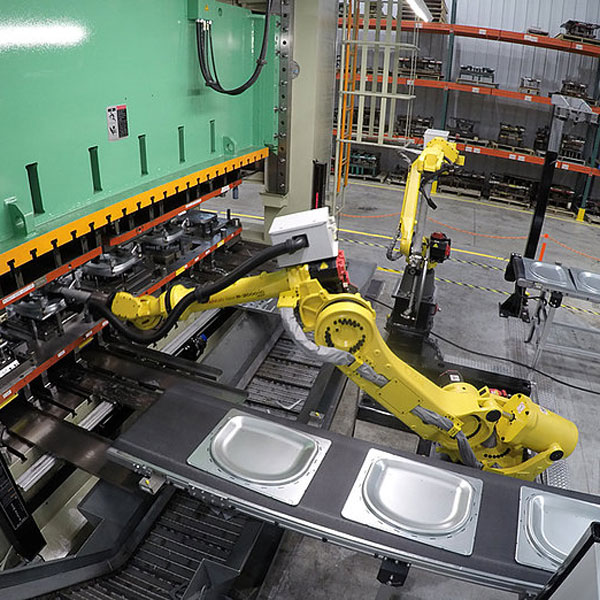
Balancing the efficiency demands with the general cost of materials is necessary to make certain the economic feasibility of the manufacturing process. By carefully evaluating these facets, makers can optimize their product selection strategies great site to accomplish premium item quality and functional performance.
Enhancing Production Performance
Performance in production processes is a crucial variable for guaranteeing cost-effectiveness and prompt delivery of high-grade steel stamped components. To improve production effectiveness in steel marking, numerous techniques can be carried out. One vital strategy is enhancing the tooling layout to decrease product waste and reduce production time. By utilizing innovative simulation software program, manufacturers can evaluate and fine-tune the tooling design before real manufacturing, therefore improving the stamping procedure and improving general effectiveness.
In addition, carrying out automation and robotics in metal marking procedures can dramatically boost efficiency and consistency while reducing labor costs. Automated systems can execute repetitive jobs with high precision and speed, resulting in boosted manufacturing efficiency and greater result prices. Investing in modern-day stamping tools with sophisticated features, such as servo-driven presses and fast die change systems, can further maximize production procedures and reduce downtime.
In addition, establishing clear interaction networks and cultivating partnership in between design, layout, and production groups is essential for identifying potential bottlenecks and implementing constant enhancements in the production process - Metal Stamping. By welcoming lean production principles and leveraging technology innovations, manufacturers can unlock the full capacity of metal find more information stamping processes and attain greater production effectiveness
Quality Assurance and Evaluation Techniques
To guarantee the constant production of high-quality metal stamped parts, strenuous quality control and examination approaches play a pivotal function in confirming the accuracy and honesty of the production process. Quality control in steel stamping involves a collection of organized checks and procedures to guarantee that each part satisfies the specific requirements. Furthermore, advanced innovations such as automated optical evaluation systems and coordinate measuring machines are progressively being used to boost the accuracy and performance of quality control procedures in metal stamping.
Final Thought
In conclusion, metal stamping offers various benefits such as cost-effectiveness, accuracy, and convenience in product growth. Generally, opening the power of metal stamping needs a tactical approach to enhance item growth processes.
Steel stamping offers a efficient and cost-efficient method for producing high-quality steel elements.Additionally, metal stamping allows for high-volume manufacturing, making it optimal for projects that call for huge amounts of metal parts.With careful factor to consider of product residential properties and geometric setups, design optimization strategies play a vital role in improving the effectiveness and functionality of steel stamping procedures.Design optimization techniques in steel stamping procedures greatly count on tactical product selection techniques to make certain the preferred performance and effectiveness of the produced components. The choice of product in steel stamping is crucial as it straight affects the quality, toughness, and total functionality hop over to these guys of the final item.
Report this page